Even though timber was never implicated in the tragedy, post-Grenfell fears around its combustibility and subsequent amendments to Building Regulations dealt a blow to timber’s credentials as the sustainable building material of choice in the UK.
These concerns, along with other persistent myths, continue to hinder the specification of timber and its wider adoption, particularly for mass timber construction. Meanwhile, sustainable design champions overseas are embracing timber’s unique qualities and properties as the standout material for low-carbon buildings.
WoodBUILD 2025 (this year taking place in Llandudno, 3 to 4 June 2025) is the annual conference and expo Woodknowledge Wales has established as Wales’ leading event for the timber industry and low-carbon housing. This year it will feature a special session co-curated with RIBA, IStructE, and CIBSE on Myth Busting - Designing and Building with Timber.
Ahead of the session, architects and other built environment professionals are invited to share their current perceptions of timber – whether informed, mythical or otherwise - by completing a short survey on myths around designing and building with timber that will help inform the upcoming debate.
Here, Diana Waldron and Clara Koehler of Woodknowledge Wales set out six persistent myths about designing with timber, and what the truths are.
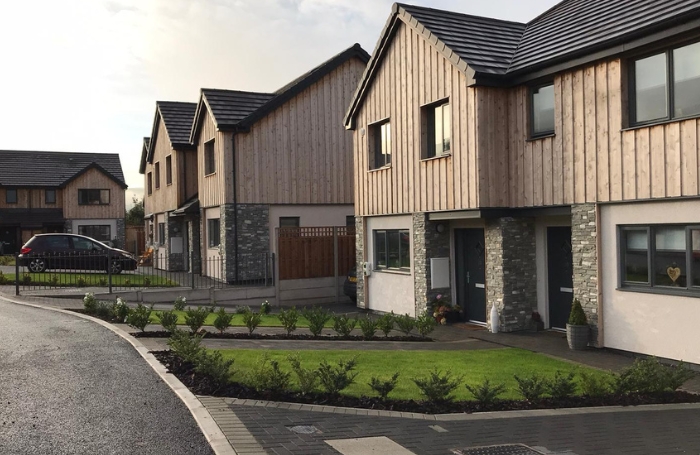
What are the myths surrounding designing with timber in architecture?
Myth 1: Timber burns easily and is unsafe in the event of a fire
Timber is a combustible material. In terms of fire safety, we need to distinguish between different applications of timber and the project context. Whether it is used as cladding, lining, or as structural elements; as well as considering the building’s typology and intended use. These contextual factors are often overlooked, yet they are crucial in determining the fire performance of timber in a specific project.
Heavy timbers char on the outside, creating an insulating layer that can protect the inner core and help to maintain the structural integrity for longer.
Amendments to Building Regulations and approved document guidance have effectively restricted the use of timber in externals walls above 11m. RIBA has recommended that further research into the use of structural timber within external walls (such as cross laminated timber) should be undertaken to obtain relevant scientific data or experimental evidence to determine and quantify the performance of buildings constructed using structural timber when subject to real fire loads. This research may be used to provide guidance to the industry though updates to Approved Document Part B and inform any changes to Building Regulations.
If we are serious about decarbonising the built environment, then a conversation is needed on how and what to build with timber rather than whether to build with timber more generally.
Read more about this in the Mass Timber Insurance Playbook.
Myth 2: Timber is less durable than steel or concrete and won’t last as long
Many cherished historic buildings are made from timber and they are still standing today. Durability of timber depends very much on the design of the building and requires a specific construction management and maintenance regime. This is known as “structural timber protection” ("konstruktiver Holzschutz" in the German-speaking world).
As a rule of thumb for any building product made from timber - whether you’re talking structure or windows or cladding - the ‘4Ds’ apply:
- Deflection: prevent water from entering the envelope in the first place,
- Drainage: provide ways for water that does get in to drain away,
- Drying: make the building breathable so any vapour can dry out,
- Decay Resistance: apply appropriate treatment where necessary.
Read more about structural timber durability.
Myth 3: Timber windows are expensive, high maintenance, and less durable than uPVC windows.
Windows provide an outlook on the world- they help set the tone and character for a building and the area in which it stands. Windows define natural lighting levels and thermal comfort essential for the wellbeing of residents and offer sound protection and keep homes safe from intrusion. Windows are an essential part of the building fabric and as such contribute to a development’s overall energy performance.
Modern factory-finished timber windows have better environmental performance than any other window material, with a longer service life and lower whole life costs than uPVC windows. Wooden windows can also be repaired and recoated throughout their lifetime and are the best option for achieving zero-carbon buildings. In addition to all this, they are also less toxic in their manufacturing, recycling, and in case of a fire.
They do come with higher upfront costs, but the multiple benefits wooden windows deliver over their life-span in terms of maintenance, durability, embodied carbon, and other social and environmental aspects make them excellent value for money.
Read more on how to specify wooden windows.
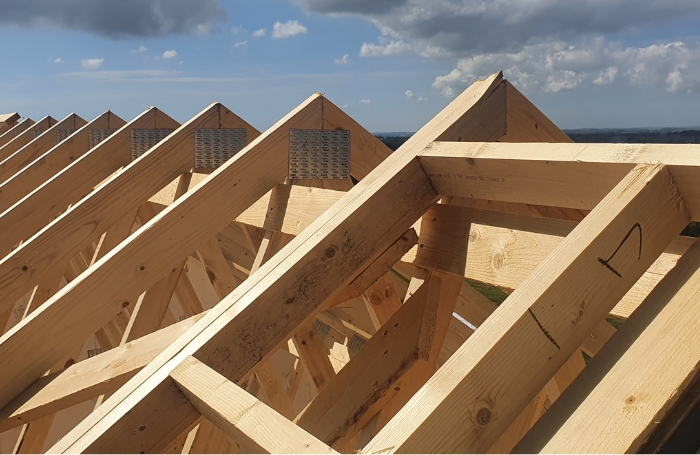
What are other myths when designing with timber in architecture?
Myth 4: Timber buildings are prone to overheating.
Regardless of the material choices, new homes often fail to meet low-energy targets and to provide summer comfort. Routine Building Performance Evaluation (BPE) is still lacking across most projects, making it difficult to address the well-known performance gap between design targets and delivery. A step change is needed to transition to low-carbon homes that are not only energy-efficient but also comfortable, healthy and enjoyable - BPE can play a significant role in achieving this goal.
To facilitate this step change, we need to embed building performance throughout the project stages and empower project teams to deliver high performance.
Natural fibre insulation, such as wood fibre, can be a good choice for achieving breathable, healthy buildings that provide thermal comfort all year-round.
Read more on how to integrate a holistic BPE approach across all RIBA stages.
Myth 5: Timber buildings are risky and hard to insure.
Concerns over fire safety, moisture risks and regulatory barriers in timber construction often stem from outdated knowledge. Modern engineered timber systems - including mass timber products like CLT (cross-laminated timber) - achieve outstanding fire performance, airtightness and thermal insulation.
Moreover, the Future Homes Standard (2025) and increasing embodied carbon requirements make timber the standout solution for low-carbon buildings. Barriers such as finding contractors or structural engineers familiar with timber systems are real, but diminishing rapidly as the knowledge and capacity within the sector expand.
Read about the Mass Timber Insurance Playbook as a finalist for the Fire Resilience Award and learn more about the timber in construction roadmap response.
Myth 6: Locally grown timber is poor quality and unsuitable for construction.
The perception that Welsh and British-grown softwoods are inferior lingers stubbornly, despite overwhelming evidence to the contrary. Species such as Douglas fir and Sitka spruce, cultivated in Wales’ temperate climate, deliver timber with comparable - and often superior - structural properties to their imported counterparts.
Thanks to advanced silviculture, consistent growth rates and improved grading techniques, Welsh-grown timber can now meet stringent structural standards. Large-diameter Douglas fir, grown in North Wales, matches high-grade imported timbers both in stiffness and durability. Misunderstandings often stem not from the timber itself, but from historic supply chain biases and a lack of targeted product development (Discover the role of conifer forests for building a sustainable society).
Find out more about the Woodbuild conference and book tickets.
Thanks to Diana Waldron and Clara Koehler, Woodknowledge Wales
Text by Neal Morris. This is a Professional Feature edited by the RIBA Practice team. Send us your feedback and ideas.
RIBA Core curriculum topic: Sustainable architecture.
As part of the flexible RIBA CPD programme, professional features count as microlearning. See further information on the updated RIBA CPD core curriculum and on fulfilling your CPD requirements as a RIBA Chartered Member.