Timber has a key part to play in the future of sustainable construction: it is a versatile building material, is relatively lightweight and has a low embodied carbon content.
But there are many considerations to bear in mind when employing timber in a design, such as which parts of a building are best suited to it, issues related to durability and moisture, and several practical and regulatory aspects that interest clients and insurers.
Consider moisture risks for maximum durability
“In the UK climate, timber can essentially last forever as long as it is kept dry,” enthuses Andrew Lawrence, “and this applies to any species of wood.”
Lawrence is Global Timber Lead at ARUP and an enthusiastic advocate for structural timber. In a previous RIBA feature, he explained how timber can truly excel in a building’s design. While moisture is something that should be addressed wherever timber is used, this is no reason not to employ timber: Lawrence can point to healthy timber structures that are approaching 1,000 years old.
Any material requires an understanding of its performance in different contexts but moisture is a prime consideration for timber. As architect Joe Giddings - who is Projects and Campaigns Director of the Timber Accelerator Hub - points out, moisture sensors can be installed in cross laminated timber (CLT) structures. Leak detection systems can be put in place which, in addition to simple design considerations, can make timber an extremely durable option.
Bringing in a specialist consultant at RIBA Stage 2 or earlier is a sensible move, as they can provide a moisture strategy to follow.
Keep dry during construction, stay dry after construction
Keeping wood dry, Lawrence points out, includes limiting any wetting during construction. Build in drainage holes and falls, he suggests, and lift walls up on plinths. If wood does get wet during construction, find a strategy to dry it out, ensuring the wood can breathe: do not stick a waterproofing barrier straight onto it, which can trap moisture.
Think about the risks of wetting to external walls or roofs in the permanent condition. Lawrence recommends providing two lines of defence: your first waterproofing barrier could eventually fail simply due to age. Ensuring the wood can breathe on all faces is a good second measure.
“Avoid any risks of water traps and ponding in your design,” Lawrence states. “If water is allowed to sit, it will quickly soak in.”
Exposed end grain is especially susceptible as it soaks up water, stays wet and then rots. This can be avoided by capping it or sealing it with an end grain sealant.
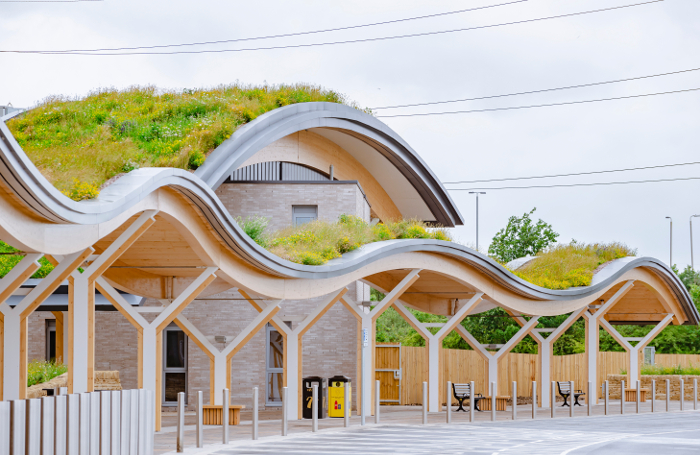
Roof considerations
Avoid flat roofs. Lawrence points out that flat roofs made of CLT are particularly vulnerable because water during construction (or due to a leak) can sit on top of it as the lines of glue can make it impermeable. Ben Price, Technical Manager at timber specialist contractors B&K Structures echoes this point.
“Ensure there is a structural fall to ensure a positive route for drainage in the event of failure of a membrane,” Price suggests. “As an additional benefit this will usually reduce the costs of insulation.”
Price also advises against the use of blue roofs (sustainable drainage systems) with CLT. While he does not rule out green roofs, he suggests that the design should allow ways for the condition of the waterproofing, and therefore the CLT, to be monitored.
Walls, balconies and terraces
It is essential that the foot of walls and columns are at least 150mm above external ground level, states Price. This might also need to apply to terraces. He suggests consideration of whether a fall could be introduced to terraces. A designer should ask themselves what the consequences of waterproofing failure in any terraces would be: would another material be more appropriate?
Price does not recommend using CLT for balconies. If they are, he suggests that they should be of the “clip-on” type, so that the external wall cladding runs between the CLT and the balcony; protecting the CLT from water seeping in.
Lawrence points out that vertical cladding will generally weather better than horizontal, as the water can quickly drain off. He suggests lifting the base of cladding 200mm above the splash zone.
Fire safety and insurance concerns
“The evidence being accrued from rigorous testing suggests that it is very safe to build with mass timber,” states Joe Giddings. He recommends engaging two fire engineers as best practice, with one to peer review the fire design. This could improve the likelihood of approval from Building Control.
There are extra measures that may or may not be necessary, depending on the context. Encapsulating the timber might be appropriate, or avoiding timber in the structural core. Giddings suggests consulting the Structural Timber Association (STA), which provides a wealth of guidance. Of particular interest is the STA’s Structural timber buildings: Fire safety in use guidance, which provides essential background and guidance for fire compliance, graded to building size and “consequence class”.
Both Giddings and Price advise bringing in the fire engineer at an early stage of the design. Indeed, they also advocate inviting an insurance broker representative from RIBA Stage 2.
“The insurer can then take part in conversations while the building’s design is being formulated,” Giddings points out. “They can see that the ‘golden thread’ is being put in place.”
Thanks to Andrew Lawrence, Director and Global Timber Lead, Arup; Joe Giddings, Project & Campaigns Director, Timber Acceleration Hub; and Ben Price and Andy Goodwin, Technical Manager and Managing Director, B&K Structures.
Andrew Lawrence will be speaking at Smart Practice 2021: Stepping up to the climate challenge on 30 September 2021. Tickets are available now.
Learn more about working with cross laminated timber by reading Cross Laminated Timber: A design stage primer by Nic Crawley, published by RIBA books.
Text by Neal Morris. This is a Professional Feature edited by the RIBA Practice team. Send us your feedback and ideas
RIBA Core Curriculum topic: Sustainable Architecture.
As part of the flexible RIBA CPD programme, professional features count as microlearning. See further information on the updated RIBA CPD core curriculum and on fulfilling your CPD requirements as an RIBA Chartered Member.
First published Thursday 16 September 2021